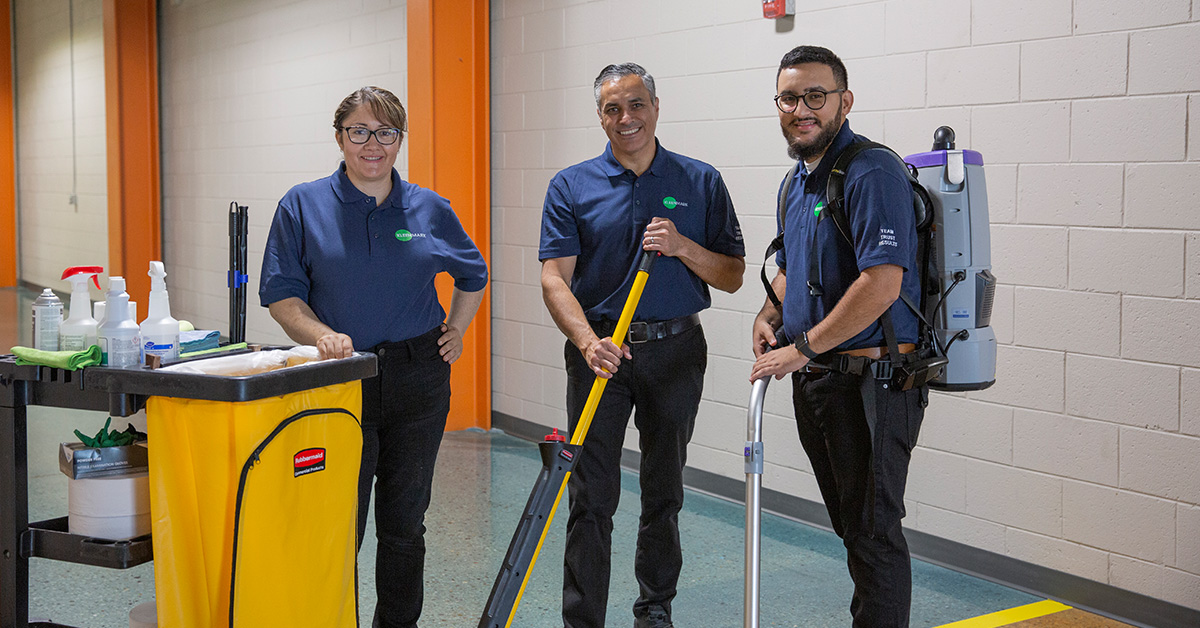
A cleaner calls in sick. You constantly have to check in on the janitorial team. The list of issues you can face when managing a manufacturing facility is long – but those related to cleaning don’t have to be on your list.
And frankly, those types of issues shouldn’t be on your list if you work with a commercial cleaning company. Instead, you should be able to focus on keeping machinery going, updating equipment and overseeing larger daily issues that arise.
We caught up with Brian Regnart, a KleenMark branch manager, to learn more about how our specially trained manufacturing teams stay on top of the toughest jobs, while freeing up a facility manager’s time and energy.
Question: One big issue we hear about is facility managers not having a backup plan for when cleaners call in sick. How does KleenMark address that?
Answer: We have a couple different approaches. First, we have technicians who can float between different accounts and facilities. They’re trained for an array of jobs and can quickly jump in if another cleaner calls in sick.
But there’s more. On top of that, our supervisors are all trained as cleaners and can easily jump in and help. We also staff with some redundancy to ensure there are enough people on hand to cover for anyone who is ill.
Q: How can facility managers stay on top of cleaning without micromanaging and wasting loads of time?
A: We’re able to provide weekly inspection reports via a digital dashboard. This allows facility managers to have clear insight into what’s been cleaned and when. Any needs or issues also are included.
Q: How does KleenMark keep unexpected janitorial needs – such as spill cleanup – from becoming an issue for facility managers?
A: We have a dedicated account manager for each of our clients. They’re readily available via phone, text, email, carrier pigeon or even the bat signal. For a facility manager, an unexpected cleaning need should never become a significant issue or problem for them.
Q: How can a facility manager at a factory feel confident they don’t need to constantly be checking in on a cleaning team?
A: Well, for us, all our cleaners receive training specific to the manufacturing facility they’ll work in. With a dedicated Health, Safety & Training Manager, we’re well versed in OSHA regulations and more.
On top of that, we spend additional time training on chemicals, cleaning frequency, which equipment to use and areas of focus. For instance, in factories restrooms and breakrooms can take a beating, so our crews clearly understand they will need to clean them more frequently than in an office, for instance.
Q: Why not just have production staff clean the manufacturing plant?
A: We’ve seen several instances where manufacturers pull people from their regular job, whether that’s on the line, running a forklift or something else, to clean. First, they aren’t properly trained, so it’s likely they’re less efficient and less effective. Second, when you pull someone from the line, you’re impacting productivity – and that’s just one more headache for a facility manager.